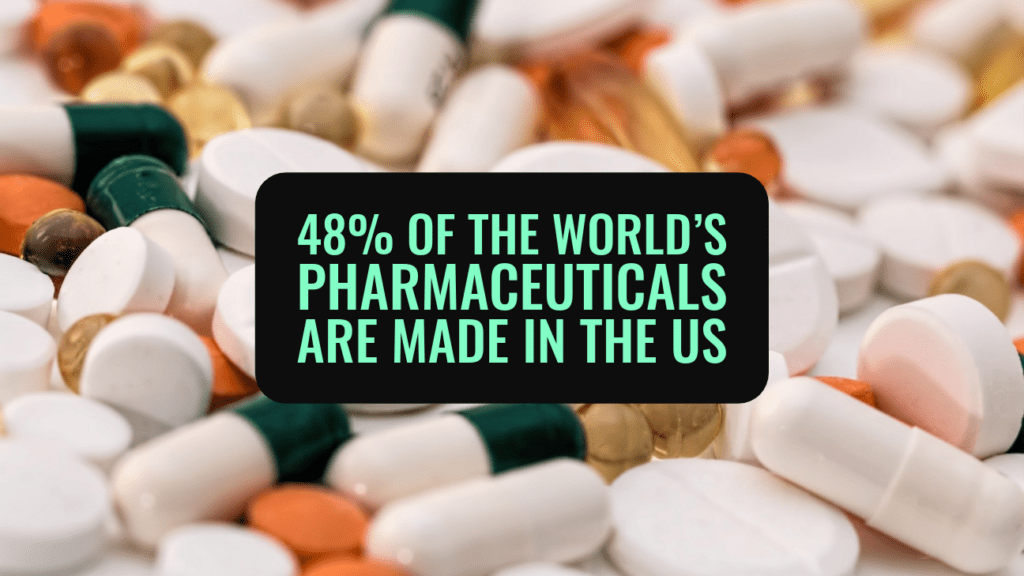
Currently, the United States is responsible for 45% of the pharmaceutical market worldwide. With respect to this, GMP storage conditions are especially important in this industry. At a glance, GMP is a system that works to ensure that products are consistent and controlled with respect to quality standards. In the pharmaceutical industry, this helps minimize the risk of contamination and potentially dangerous mixups with products.
GMP quality control oversees the entire process of manufacturing from start to storage. This includes the materials, the condition of premises, the equipment used for manufacturing and synthesis, and the hygiene standards of the staff. Throughout these processes, systems must be in place to document the steps as proof of compliance, each and every time the process is repeated.
While there are many different points that can be covered, here we’ll be covering GMP storage conditions and the basics of following this set of GMP standards.
GMP Storage Conditions
- A couple of the largest points include:
- No unauthorized persons are allowed within GMP storage areas.
- The capacity of storage areas should be sufficient enough to allow the orderly storage of materials in their respective places.
- Storage locations should be clean, dry, and temperature controlled to ensure the quality of goods and prevent degradation. If products have special requirements they should be labeled appropriately and monitored regularly.
- Sanitation logs should be kept in storage locations to ensure the area is kept clean and vermin free. Vermin could contaminate and cause damage to stored products making pest control an essential part of GMP quality assurance. Likewise, spills and leaks should be reported and cleaned to prevent harm or cross-contamination.
- Quarantine areas must be clearly marked and access should be highly restricted to prevent unauthorized entry.
- Sampling areas should be separated and marked in a controlled environment. All sampling should be conducted in a manner that prevents cross-contamination between samples. Cleaning protocols should likewise extend to these areas.
- Expired, recalled, or otherwise invalidated materials should be segregated and labeled properly.
- A dedicated area should be assigned to substances that are narcotics, radioactive, or otherwise hazardous. This extends to substances that pose fire risks, such as pressurized or combustible liquids.
- When handled, care should be taken with products to ensure no contaminations or mix-ups occur.
- FEFO (first expired - first out) should be followed during storage. Materials should be stocked and rotated accordingly to ensure the highest quality.
- Narcotics and other controlled substances should be stored in a way that complies with international and federal conventions, laws, and regulations.
- Broken products should be labels, documented, and separated from the rest of the stock.
- Adequate lighting should exist throughout the facility.
The above is the most basic GMP storage condition requirements as stipulated by the World Health Organization. To ensure the continued quality of your pharmaceutical products, these and all GMP standards should be heeded, followed, and implemented in your storage facilities.