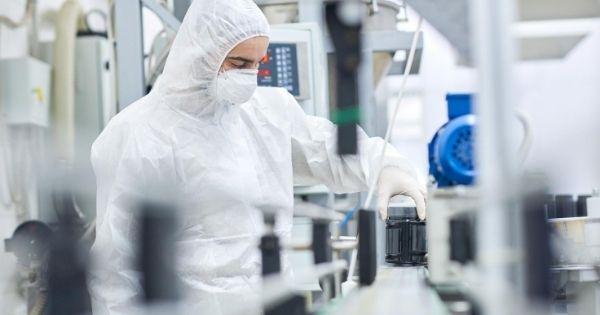
Every workplace presents a unique set of dangers. The pharmaceutical manufacturing industry presents many risks, from manufacturing-specific considerations to pharmaceutical safety hazards. While health and safety can often be difficult to maintain, the pharmaceutical industry must follow safety standards and regulations. From basic protections to highly specified pharmaceutical precautions, pharmaceutical manufacturing safety considerations cannot be overlooked.
Practice Basic Laboratory Safety
When working in any type of laboratory, following basic laboratory safety is a necessity. The Occupational Safety and Health Administration (OSHA) provide detailed guidelines on laboratory safety. For laboratory workers, these guidelines should be second nature. A few of the guidelines include:
- Quickly clean up all spills
- Maintain a tidy work area
- Frequently wash hands
- Wear a laboratory coat
- Never smoke inside the laboratory
- Label containers correctly
- Wear eye protection and other personal protective equipment (PPE)
- Do not wear clothing that exposes the skin (eg, shorts and T-shirts)
- Do not eat in the laboratory
- Regularly check that glassware is not cracked and that all equipment is safe to use
- Keep entryways clear
These safety standards apply to any laboratory and can be altered to adhere to pharmaceutical work specifically. Follow these practices as well as basic manufacturing practices like maintaining and using the proper equipment. Besides basic laboratory safety and manufacturing safety measures, there are many more safety standards for pharmaceutical manufacturing sites. Here are a few other suggested pharmaceutical manufacturing safety considerations.
Perform Risk Assessments
Risk assessments work to identify and analyze any potential events or substances that may negatively impact individuals, products, or the surrounding environment. Risk assessments aim to scale the level of risk present to determine if any event or substance needs to be altered or eliminated. The pharmaceutical manufacturing industry presents unique risks to employees due to the increased likelihood of interacting with hazardous chemicals. Performing regular and frequent risk assessments is one of the best ways to keep pharmaceutical manufacturers safe.
OSHA monitors workplaces to ensure risk assessments are carried out properly. All potential safety hazards a pharmaceutical manufacturer might face should be assessed based on OSHA regulations to determine if they are met or if a change needs to be implemented to limit risk. Below is the five-step system that is followed for a risk assessment:
- Try to identify any potential hazards by walking around the working area. Look up potential dangers based on OSHA’s recommendations and examining accident record sheets.
- Next, note who may be at risk as a result of any dangers identified in step one. For example, transportation workers may be at risk due to improper identification and harmful chemicals stored during transportation.
- The third step is to take action and decide how the hazards need to be dealt with. Legally, the risk must either be removed or minimized. Limited access to a hazard or eliminating the hazard altogether is one of the best ways to take action.
- The previous steps should be recorded, including documenting what the risk was and what action was taken. This gives a detailed record of how the hazard was addressed for future reference.
- Lastly, review the assessments annually to make sure that safety measures are being maintained in the workplace.
Keep Material Safety Data Sheets
Pharmaceutical companies commonly work with hazardous chemicals that can put any handler at risk. Material safety data sheets contain information about the chemical or other substances being used. The safety data sheet should provide identification of the chemical or substance and the provider's contact information, identification of the hazards present, the composition and ingredients, a toxicology report, first-aid measures, handling and storage instructions, disposal information, and personal protection requirements. A material safety data sheet should always be present when working with chemicals. OSHA’s Hazard Communication Standard requires that chemical suppliers provide manufacturers with a safety data sheet. Always request a safety data sheet if it is not given and keep them easily accessible to pharmaceutical manufacturing employees at the appropriate workstation.
Document, Document, Document
Aside from following material data sheet documentation and risk assessment documentation, detailed notes should be taken of all steps in the manufacturing process. Documentation should be kept so that all processes are safely followed the same way each time. With the combination of risk assessments and other precautionary measures like outlining PPE requirements, a detailed description of the manufacturing process can include specific instructions for avoiding unsafe protocol. The documents can also be used as a reference when hazards do arise to determine where in the process changes need to be made.
Chemical Handling
As previously mentioned, chemicals are a common component of pharmaceutical manufacturing. Chemical handling can be highly dangerous due to the increased risk of fires, explosions, and the release of harmful toxins. The transportation, handling, and use of toxic substances should also be as safe as possible and risks should be eliminated or reduced when possible.
Like Safety Data Sheets, the Globally Harmonized System of Classification and Labeling of Chemicals (GHS) can be used to identify and explain the harm present with each chemical. The system also highlights how to properly store, label, and move chemicals to minimize the risk of a dangerous event such as a fire occurring.
Safety Equipment for Chemical Handling
Personal Protective Equipment (PPE) such as gloves and eye protection should always be worn. Safety equipment such as an emergency safety shower or an eyewash station is another must-have safety consideration. While PPE should be the frontline method of protection, these are tools that can be used to clean any chemicals off the eyes, skin, or clothing to minimize long-term damage from coming in contact with unsafe materials in case a hazardous event occurs.
Maintaining safety can be difficult for pharmaceutical manufacturing companies. Not only do companies have to be mindful of basic manufacturing safety compliance, but they must also be mindful of pharmaceutical considerations. The best way to maintain a safe pharmaceutical manufacturing facility is to keep up with regulatory standards put in place by organizations like OSHA. Consistently relying on basic laboratory safety precautions, performing risk assessments, keeping material safety data sheets, providing further documentation, and properly handling chemicals is the best way to maintain pharmaceutical manufacturing safety measures.
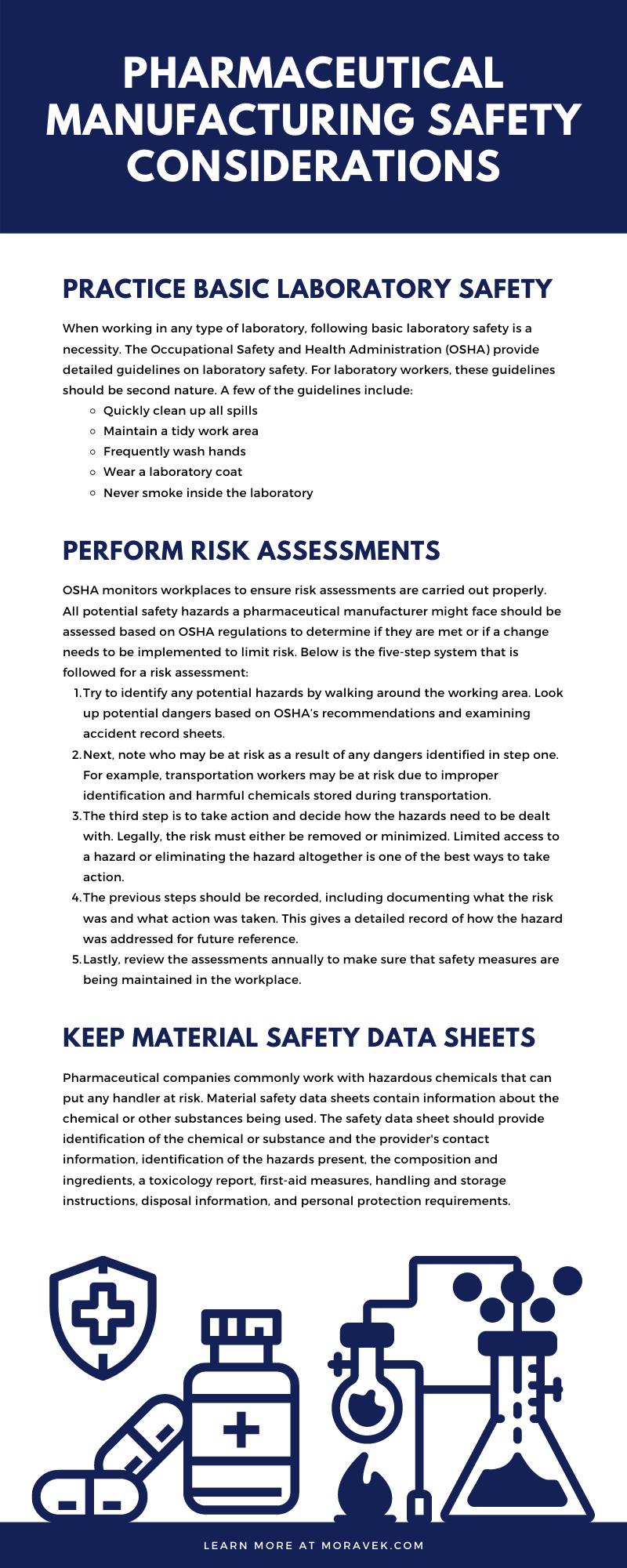